Well if you are ready for this awesome YouTube video click the link - but srsly as the title suggests it is pretty scripted and well - bad.
Link
It does show us a nice case study of a big industy player using solidworks and printing their design concepts on a daily basis - what more could we ask for?!
Monday, 1 November 2010
Sunday, 24 October 2010
3D printing Bandi Japan
http://www.youtube.com/watch?v=6bgfbteTLfY&feature=related
Mental video
I think we should adopt their work cloths
Mental video
I think we should adopt their work cloths
Labels:
3D printing,
Case Study,
CNC,
Feature,
General,
Machining,
Software,
tutorial,
Video
1:1 zbrush figure print
Hows this for size!
a 7ft video game charictor modled in z brush and printed in an unknown amount of pieces!
via
http://www.zbrushcentral.com/showthread.php?t=88937
a 7ft video game charictor modled in z brush and printed in an unknown amount of pieces!
via
http://www.zbrushcentral.com/showthread.php?t=88937
Labels:
3D printing,
Installation,
Machining,
Software,
Video
Thursday, 21 October 2010
check it
http://design-milk.com/deconstruction-cell-cycle-by-nervous-system/
and
http://n-e-r-v-o-u-s.com/cellCycle/index.php
enjoy @_@
and
http://n-e-r-v-o-u-s.com/cellCycle/index.php
enjoy @_@
Wednesday, 20 October 2010
Skydrive
Hello all -
A reminder that all work to be done on the lasers require you to have had your files checked and are then uploaded onto your skydrive. No USBs on the laser PCs :)
happy lasering xx
A reminder that all work to be done on the lasers require you to have had your files checked and are then uploaded onto your skydrive. No USBs on the laser PCs :)
happy lasering xx
TCT Live 2010
Woop what a day - most spent in a car but some was spent at the awsome TCT live in Coventry.
Check out the Set on FlickR
Not much has changed from last year, machines have gotten smaller still and resolutions are getting higher. Things are getting cheeper but still out the reach of us poor people. :(
Labels:
3D printing,
Case Study,
CNC,
Digitising,
Engraving,
Feature,
General,
Lasers,
Machining,
Software
Jobbage
After many months of getting things right - I got a big job from Dayfold to cut 500 peices of red paper.
Lots of overtime later and a borrowed laser from our lovely friends at Textiles, we got the job done with minuets to spare!




I look forward to seeing the folded sleve.
Lots of overtime later and a borrowed laser from our lovely friends at Textiles, we got the job done with minuets to spare!
I look forward to seeing the folded sleve.
Labels:
Case Study,
Engraving,
Illustrator,
Lasers,
Machining
Super glue spray fail
superdrug's spray dispensers don't work with super glue.
I got around 3 pumps before the stupid thing stuck itself together.
those three pumps looked promising though - I ended up dropping glue onto the model - it was a pain in the proverbial but gives quick and durable results.
If you have a day to spare while the thing cures I would recommend using resin due to the infiltration qualities. Edit - Superglue FTW more costly but srsly its where its at!
Labels:
3D printing,
Case Study,
General,
Machining,
Rhino,
Software,
tutorial
Tuesday, 5 October 2010
Will's Flywheel
At it again - Will is making bits for his trains.
This time we went for a 'case study' appraoch and flexed our brain muscles for a bit of a challenge.

After seeing things like this on the web and print brouchures we thought we would give it ago outselves.
Solidworks still being new to us, I went in and drew up a fly wheel which overall was pretty simple - I did draw it three times before we were satisfied however!

Using the mould tools integrated into solidworks - and several hours of trying to figure things out we got our two peice mould, made a quick STL and off we went to the printer.


So when all the prints were out - cleaned off with the air but we were impatant and took it out before they had finnished being baked in the machine - so we transfered them into the oven upstairs for a blast for around 30 mins.

Being a bit of a noob the pour hole was a little small - so I countersunked it to enlarge - and maskeing taped the two halves together. We then embeded it into the sand pit ready for a pour.



And the pour..

After a short period to let the pewter cool - we got the part out the sand and peeled off the tape.
We were suprised of the weight - assuming things must have gone what right for us!

Hitting it with a hammer - the only solution for a stuborn mould!

After a demoulding by hammers - scrapers and a quick sandblast we have the part!!

And the money shot:
This time we went for a 'case study' appraoch and flexed our brain muscles for a bit of a challenge.

After seeing things like this on the web and print brouchures we thought we would give it ago outselves.
Solidworks still being new to us, I went in and drew up a fly wheel which overall was pretty simple - I did draw it three times before we were satisfied however!

Using the mould tools integrated into solidworks - and several hours of trying to figure things out we got our two peice mould, made a quick STL and off we went to the printer.

So when all the prints were out - cleaned off with the air but we were impatant and took it out before they had finnished being baked in the machine - so we transfered them into the oven upstairs for a blast for around 30 mins.
Being a bit of a noob the pour hole was a little small - so I countersunked it to enlarge - and maskeing taped the two halves together. We then embeded it into the sand pit ready for a pour.
And the pour..
After a short period to let the pewter cool - we got the part out the sand and peeled off the tape.
We were suprised of the weight - assuming things must have gone what right for us!
Hitting it with a hammer - the only solution for a stuborn mould!
After a demoulding by hammers - scrapers and a quick sandblast we have the part!!
And the money shot:
Labels:
3D printing,
Case Study,
Feature,
Machining,
Software,
Solidworks,
tutorial
Monday, 4 October 2010
Solidworks more like solid wtf how do you get this to work?!
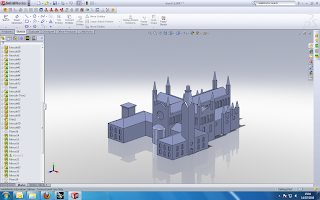
So yeah new year new software installed - we have an academic licence of Solidworks and CAMWorks - here's to hoping you already know how to use them!
Solidworks is pretty hot - I have been playing with it for a month or two now and getting the hang of it more, the more I use it. I actually really like it - it feels more intuitive than Rhino - in fact I barely open rhino any more other than drafting for the laser.
CAMWorks on the other hand though is something else - even getting the thing to load and find the licence is something like voodoo.
It should be a great product that seamlessly links 3D solid modeling with CAM and our Mill - so far its just making nice 3D digital models with no cam any time soon.
What this post was meant to be about....
I did manage to get a few models 3D printed here is my favorite!
Yes, it is a pink cathedral
Labels:
3D printing,
Case Study,
CNC,
Feature,
General,
Machining,
Software,
Solidworks
Yeah new term
Hi Everybody!
Welcome back and a big hello to all the noobs joining us this year!
Lets kick some ass!!
Welcome back and a big hello to all the noobs joining us this year!
Lets kick some ass!!
Wednesday, 7 July 2010
Bartlet Architecture Final Show UCL
Walking from Waterloo to UCL took just over an hour - but we got to see alot of London's back streets that would have been missed if we took the tube. The day was hot despite staring out with rain, and not taking the most direct rout at times just made things worse. Anyway - by 2:30 we had made it, and the courtyard of UCL was a little sancuary in the middle of hell that was london, quiet and calm, we were met with this.

In the right place then.
The show was pretty large accutally, spanning several rooms with a range of work in each. Models were everywhere which was a plus for me - and they were getting alot of attention from everyone else in the gallery.




To go with the countless models were collections of artwork which as an outsider I coulnt see the relevence to an Architecture degree show but they were stunning none the less - very sci fi.





The models on show had a range of technologies applied to them - predominently Dprinted with elements of lasercut acrylic. I spoke toone of the students on hand and asked about the software used to create such generative forms. They all get introductions into Rhino, Solidworks, Studio MAX - even google sketchup is used extensivly. He also explained that they build several models digitally - some for specification and also some specifically for the use of prototyping technologies. All models are brought and payed for at a little above cost.










Overall the day was great and well worth the treck accross London town to get there! The level of work - and the quality and extensiveness of the 3D prints was a great thing to witness!! Some of the aplications were questionable, such as a printed landform, but over all the applications were very generative and testament to their skills on CAD. Some of the details were very fine and bridging[from my persective] the gap between technology and art.
In the right place then.
The show was pretty large accutally, spanning several rooms with a range of work in each. Models were everywhere which was a plus for me - and they were getting alot of attention from everyone else in the gallery.
To go with the countless models were collections of artwork which as an outsider I coulnt see the relevence to an Architecture degree show but they were stunning none the less - very sci fi.
The models on show had a range of technologies applied to them - predominently Dprinted with elements of lasercut acrylic. I spoke toone of the students on hand and asked about the software used to create such generative forms. They all get introductions into Rhino, Solidworks, Studio MAX - even google sketchup is used extensivly. He also explained that they build several models digitally - some for specification and also some specifically for the use of prototyping technologies. All models are brought and payed for at a little above cost.
Overall the day was great and well worth the treck accross London town to get there! The level of work - and the quality and extensiveness of the 3D prints was a great thing to witness!! Some of the aplications were questionable, such as a printed landform, but over all the applications were very generative and testament to their skills on CAD. Some of the details were very fine and bridging[from my persective] the gap between technology and art.
Labels:
3D printing,
Case Study,
CNC,
Digitising,
Feature,
General,
Installation,
Lasers,
Machining,
Paneling Tools,
Pattern,
RhinoCAM,
Software,
Solidworks,
Spraying,
tutorial
Tuesday, 29 June 2010
Engraving Duo Plan
Working closely with Dayfold Print, we have been trying hard to achieve the best possible finish on their new Duo plan and Tri plan card stocks.
These A5 sample cards show the range off effects just by choice of colour.

Black on yellow


The process works great on block fills as well as text

A macro of the high detail border

Blue on black

A perfect surface finish despite the deap engrave

Black on blue, showing a nice embossing feature of the process


Striking yellow on black surface

The vibrancy of yellow is kept during the process

The yellow on black is one of the more attractive card stocks, and leant its self well to being laser engraved.
Each sample measures 200mm x 140mm and took little over 10 minuets to complete. Due to the engraving process, the complexity of the data shouldn't slow the process down. The finish required by Dayfold and the material properties meant that the laser had to run at less than optimum performance to vaperise the first layer of material. Power was at 100% speed running at a slower 50%.
for more information contact either myself or Chris@dayfold.com to help you realise your idea.
These A5 sample cards show the range off effects just by choice of colour.
Black on yellow
The process works great on block fills as well as text
A macro of the high detail border
Blue on black
A perfect surface finish despite the deap engrave
Black on blue, showing a nice embossing feature of the process
Striking yellow on black surface
The vibrancy of yellow is kept during the process
The yellow on black is one of the more attractive card stocks, and leant its self well to being laser engraved.
Each sample measures 200mm x 140mm and took little over 10 minuets to complete. Due to the engraving process, the complexity of the data shouldn't slow the process down. The finish required by Dayfold and the material properties meant that the laser had to run at less than optimum performance to vaperise the first layer of material. Power was at 100% speed running at a slower 50%.
for more information contact either myself or Chris@dayfold.com to help you realise your idea.
Labels:
Case Study,
Engraving,
Feature,
General,
Illustrator,
Lasers,
Machining,
Pattern,
Software,
tutorial
Subscribe to:
Posts (Atom)